ATS Global
Sepasoft MES Premier Integrator
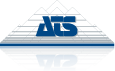
ATS is the Independent Solution Provider for Industrial, Process and Information Technology users worldwide and celebrates 30 years of providing these services to our loyal customers! We provide products and services for all three levels of the automation pyramid; control, and execution and information.
MES Certifications
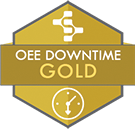
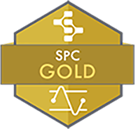
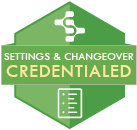
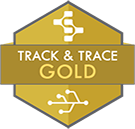
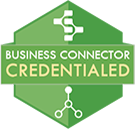
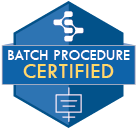
2 Gold, 7 Certified, AND 24 Credentialed MES ENGINEERS
11 LOCATIONS
Projects
SPC is now Mission Critical
US
An existing Ignition user had need to replace their third-party SPC software. The existing
An existing Ignition user had need to replace their third-party SPC software. The existing SPC solution was disconnected from the job and key information. The customer requested a pilot of the Sepasoft SPC to extend the capabilities of their Ignition implementation.
ATS jump started the customer’s capability with SPC via a rapid pilot on a few key machines. Proving the value of the module with accurate recording, tracking of data, and integration with test equipment, the customer continued a roll-out to the entire facility. As new lines go in, SPC will be extended to them. In the customer’s words: “It was well received on the plant floor...and by management. It’s now mission critical.”
ATS jump started the customer’s capability with SPC via a rapid pilot on a few key machines. Proving the value of the module with accurate recording, tracking of data, and integration with test equipment, the customer continued a roll-out to the entire facility. As new lines go in, SPC will be extended to them. In the customer’s words: “It was well received on the plant floor...and by management. It’s now mission critical.”
OEE 3.0 Pilot for Leading Packaging Company
US
The customer is a leading company in the design and manufacturing of packaging for commercial
The customer is a leading company in the design and manufacturing of packaging for commercial products with multiple sites across the US.
They wanted to start collecting OEE and downtime data from all sites and have it available in real time, both locally and from a central location.
Since all sites are of two different types, the customer wanted ATS to develop a pilot solution per site type that could easily extend to the remaining sites.
ATS completed a pilot project where two template projects were developed - one per site type - with all resources such as OEE monitoring, downtime management, dashboards, operator screen, charts, reports, and system configuration. With the project inheritance properties available in Ignition 8, ATS created a child project on each site, which inherits all resources from the template project while allowing the development of custom screens, reports, etc.
ATS also developed an enterprise project where authorized users have an overview of all sites, with drill down options to each line on any site.
In addition to the Ignition and Sepasoft work, ATS also helped the customer with the integration of legacy controllers and the installation of sensors for the MES counters.
They wanted to start collecting OEE and downtime data from all sites and have it available in real time, both locally and from a central location.
Since all sites are of two different types, the customer wanted ATS to develop a pilot solution per site type that could easily extend to the remaining sites.
ATS completed a pilot project where two template projects were developed - one per site type - with all resources such as OEE monitoring, downtime management, dashboards, operator screen, charts, reports, and system configuration. With the project inheritance properties available in Ignition 8, ATS created a child project on each site, which inherits all resources from the template project while allowing the development of custom screens, reports, etc.
ATS also developed an enterprise project where authorized users have an overview of all sites, with drill down options to each line on any site.
In addition to the Ignition and Sepasoft work, ATS also helped the customer with the integration of legacy controllers and the installation of sensors for the MES counters.
SPC Template for Multi-plant Operations
The customer faced a common issue: various papers/forms in the plants. The SOP on the
The customer faced a common issue: various papers/forms in the plants. The SOP on the shopfloor was not always in the latest version, the handwritten SPC data was sometimes difficult to read, there would be delays in compiling data due to hand processing.
ATS implemented an SPC solution which enables the customer the capability to link data from the process lines with live quality & SPC analytics. SPC alarms offer management a more interactive role with the shopfloor, including a better collaboration with engineering and maintenance. Quality authorities are now informed of their quality progress in real-time from their offices analyzing Cp, Cpk …
In the customer’s words: “SPC has meant a new world for us, from basic handmade tools to advanced process control, integrated management of real-time and historical data and quicker resolution of problems since they are detected immediately by the operator.”
ATS implemented an SPC solution which enables the customer the capability to link data from the process lines with live quality & SPC analytics. SPC alarms offer management a more interactive role with the shopfloor, including a better collaboration with engineering and maintenance. Quality authorities are now informed of their quality progress in real-time from their offices analyzing Cp, Cpk …
In the customer’s words: “SPC has meant a new world for us, from basic handmade tools to advanced process control, integrated management of real-time and historical data and quicker resolution of problems since they are detected immediately by the operator.”
OEE + WS Template for Multi-plant Operations
The implementation of the OEE module integrated within Ignition SCADA allows the plants to get
The implementation of the OEE module integrated within Ignition SCADA allows the plants to get a real time status of the production line. The addition with the ERP connectivity via the Web Services module, reduces the need of paper, allowing a more dynamic and real-time planning and control of the line. The integration with the PLC adds more accurate reasons for downtimes and timing.
With increased quality of information, management and maintenance can pinpoint and resolve issues more effectively. Various plants within the group now have the same standard way to record information and calculate OEE.
“Since the implementation of the OEE, we have improved the resolution of downtimes in the lines, acquired a better understanding of the line bottlenecks and reduced dramatically the paperwork.”
With increased quality of information, management and maintenance can pinpoint and resolve issues more effectively. Various plants within the group now have the same standard way to record information and calculate OEE.
“Since the implementation of the OEE, we have improved the resolution of downtimes in the lines, acquired a better understanding of the line bottlenecks and reduced dramatically the paperwork.”
T&T + WS Template for Multi-plant Operations
ATS implemented a system which offers to the customer the feature to track all the
ATS implemented a system which offers to the customer the feature to track all the consumed materials and the produced serialized final product through the whole plant. Ignition and Sepasoft MES modules played a key part in this solution. Merging the SCADA features, ERP interface and MES modules in one single application, easy to use for the operators, was a strategic option for this customer. The system receives the Work Orders and Bill of Materials from their ERP. The operator scans the materials while using Ignition to verify the right information vs BOM. With the use of PLC, inline Barcode scanners, each ingredient is recorded and coordinated with their production context, offering to the customer a historical traceability downstream and upstream. This solution enforced the traceability and quality of the product, as well as the end customer trust.
“Since the implementation, we have improved a lot, the identification of the different Work in Progress materials, standardizing the label ID, we have a much better visibility over the material flows (real-time status) and traceability of products sent to each customer is now possible.”
“Since the implementation, we have improved a lot, the identification of the different Work in Progress materials, standardizing the label ID, we have a much better visibility over the material flows (real-time status) and traceability of products sent to each customer is now possible.”
Locations
Fremont, California
US
39510 Paseo Padre Parkway, Suite 120
Holly Becker
Dalfsen, Overijssel
NL
PTA, Miñano, Vitoria
ES
Leonardo da Vinci, 14
Gorka Gorostiaga
Kassel, Hessen
DE
Falderbaumstraße 16
Daniel Sutter
ROCHESTER HILLS, MI
US
1055 SOUTH BLVD E STE 120
Holly Becker
Aguascalientes, Aguascalientes
MX
Av. Universidad 1005, Interior 4 Bos...
Holly Becker
Derby, DERBYSHIRE
GB
Weston House, Bradgate Park View
Jarett Lathey
Leeds, LEEDS
GB
Suite 1d/1e Brooklands Ct Tunstall R...
Jarett Lathey
Nuneaton, WARWICKSHIRE
GB
ATS House 59a Coton Rd
Jarett Lathey
Mahape, Navi Mumbai, Maharashtra
IN
1019, 10th Floor, Rupa Solitaire Bui...
Anand Rahul
Mulgrave, VIC
AU
U9, 18-22 Lexia Place
Rob Conway
Contact
Holly Becker

OEE Gold Certified
2 Engineers

OEE Certified
3 Engineers

OEE Credentialed
23 Engineers

SPC Gold Certified
1 Engineer

SPC Certified
5 Engineers

SPC Credentialed
21 Engineers

Settings & Changeover Credentialed
18 Engineers

Track & Trace Gold Certified
1 Engineer

Track & Trace Certified
4 Engineers

Track & Trace Credentialed
13 Engineers

Business Connector Credentialed
10 Engineers

Batch Procedure Certified
1 Engineer