MES Enterprise
Users can now create a global MES Enterprise, allowing them to manage Batch Procedure, OEE, Track & Trace, Settings & Changeover, and SPC data across all their worldwide facilities. Data is seamlessly synchronized from the plant floor to the executive suite, providing the capability to monitor ongoing operations, evaluate results, and conduct audits across all plants from a centralized location.
MES Platform: Enterprise Functionality
The MES Suite now offers out-of-the-box enterprise functionality across multiple Ignition® Servers. It ensures seamless automatic synchronization, delivering materials, equipment, production schedules, inventory, work instructions, and more to the right place at the right time. Production results are transmitted in real-time up the enterprise architecture, enabling live production monitoring across the entire organization.
On-Prem, on the Edge, or Scale to the Cloud
With the Ignition® Gateway Network functionality, users can create MES enterprise servers at any location within their global operations. Any Ignition® server can be designated as a member of the MES enterprise, including Ignition® Edge servers and cloud-hosted Ignition® servers..
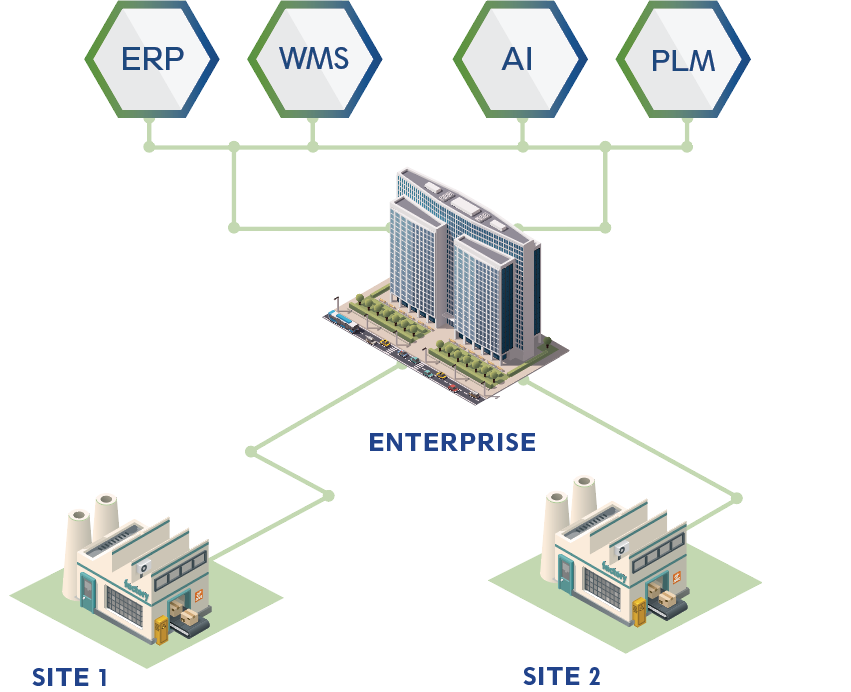
Stay in Sync Across Your Enterprise
All essential production data is automatically distributed to servers within your MES enterprise, ensuring that it is available only where needed. With simple configuration, materials, equipment, production schedules, inventory, work instructions, and more are delivered to the right place at the right time, helping to keep your production running smoothly.
Rapid Disaster Recovery
All MES configuration data is synchronized with other servers within your MES architecture providing an up-to-the-minute production data backup. This means any server within your MES architecture can be rapidly restored to production state without any loss of data. Restoring your data is as simple as connecting a new MES server. Critical future production data will automatically be restored, minimizing downtime. Additionally, the platform supports Ignition® redundancy, enabling real-time failover to backup servers seamlessly.
Track Essential Metadata with Artifacts
Using the built-in artifacts, any information essential to your enterprise can be assigned to operations, equipment, people, materials, schedules, lots, and more. The information can include, but is not limited to, work instructions, calibration records, test instructions, test results, machine settings, and much more.
The data format is flexible and includes tables, lists, images, binary data, or even PDFs and is synchronized to the correct MES server in context of the larger MES picture.
Centralized Equipment Configuration & Monitoring
The equipment architecture for your entire enterprise can be centrally configured or, depending on security settings, configured locally while modifications are automatically synchronized to the correct servers within your MES enterprise.
MES system performance can be analyzed locally or centrally. Increased granularity of performance including analysis items, MES database queries, and much more can be viewed using the new MES Monitoring Component.
Excited to learn more? Reach out to us to schedule a live demo today!
Unparalleled Value
Sepasoft’s unified MES system offers centralized configuration, resulting in increased accountability and better collaboration of production plans. With built-in synchronization of production data across the whole enterprise, both implementation time and maintenance costs are greatly reduced. MES enterprise functionality breaks the data island barriers, making production results visible at all levels of your operation in real-time, greatly speeding up the process of identifying and resolving production issues, and keeping an eye on production progress. Centralized system monitoring provides visibility of the MES architecture, including communication links, status of servers, and overall system performance to detect and resolve issues early. These features are vital for a modern enterprise-wide MES implementation.
Built on Ignition®
The MES Suite with MES enterprise functionality installs on Ignition®, the powerful, award-winning, HMI, SCADA, and industrial software platform from Inductive Automation. The MES Suite is built to help your enterprise align with ISA-95 model standards for integrating enterprise and control systems.
By leveraging the full power of Ignition®, Sepasoft® modules are unlike any other MES offering available on the market.
To learn more or to purchase MES Enterprise, contact Sales at 800-207-5506, select Option 1, or visit our pricing page