Vertech
Sepasoft MES Premier Integrator
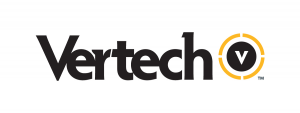
At Vertech, we believe there is a human way to do industrial automation. Yes, we design bulletproof MES, SCADA, OT, and controls solutions that are a joy to use. But we are also your long-term ally. No more endless change orders. No more paying good money for a half-solution. We are here to reduce your tech-related stress, not add to it. And who knows? You might even enjoy the process.
MES Certifications
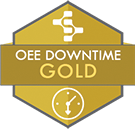
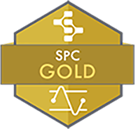
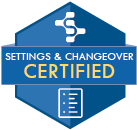
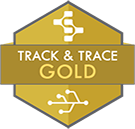
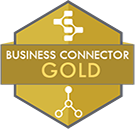
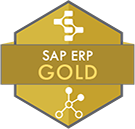
5 Gold, 8 Certified, AND 5 Credentialed MES ENGINEERS
4 LOCATIONS
Projects
OEE 1.0 to OEE 2.0 Conversion
US
The scope of this project was to migrate an existing OEE 1.0 application to an
The scope of this project was to migrate an existing OEE 1.0 application to an OEE 2.0 application. A new OEE 2.0 base project was created, complete with a new production model for a single line.
The new production model had 30 objects with a complex mixture of cell groups and cells within a single process line. Visual elements, windows, templates, and scripting functions were exported from the original OEE 1.0 application and brought into the new OEE 2.0 application. New templates, scripts, and components were created to take advantage of new methods and features available in OEE 2.0.
The original OEE 1.0 system also included Recipe Management and SPC functionality. The Recipe and SPC modules were integrated with OEE 2.0 to automatically generate the proper material definitions from recipes prior to starting production run.
The primary value-add of OEE 2.0 was an improvement in downtime tracking across the complex line configuration. New downtime summary screens were created as well as a script package to evaluate downtime reason code and equipment changes initiated from remote, non-Ignition operator terminals. This is critical in determining if downtime events are new, changed, or reassignments and how to manage the downtime event records without the operator having to travel to the primary Ignition client.
The new production model had 30 objects with a complex mixture of cell groups and cells within a single process line. Visual elements, windows, templates, and scripting functions were exported from the original OEE 1.0 application and brought into the new OEE 2.0 application. New templates, scripts, and components were created to take advantage of new methods and features available in OEE 2.0.
The original OEE 1.0 system also included Recipe Management and SPC functionality. The Recipe and SPC modules were integrated with OEE 2.0 to automatically generate the proper material definitions from recipes prior to starting production run.
The primary value-add of OEE 2.0 was an improvement in downtime tracking across the complex line configuration. New downtime summary screens were created as well as a script package to evaluate downtime reason code and equipment changes initiated from remote, non-Ignition operator terminals. This is critical in determining if downtime events are new, changed, or reassignments and how to manage the downtime event records without the operator having to travel to the primary Ignition client.
OEE for 13 Critical Process Lines
Eastern US
The scope of this project was to provide OEE and downtime tracking in real time
The scope of this project was to provide OEE and downtime tracking in real time to an operation that was tracking OEE manually each hour. The final product included tracking for 13 critical process lines throughout the fabrication and finishing operations within the facility. The production model includes 161 objects with each process line ranging from having no cells to a complex mixture of cell groups and cells. Due to the nature of different integration points in the facility, 4 lines took advantage of the “Tag-based OEE” option provided by the module while the other 9 lines utilized the module’s standard ISA-95 model implementation.
Two Ignition projects were used to separate the ‘operator’ and ‘management’ functions of the application. The operator project includes features such as: starting and stopping production runs, setting downtime reason codes, and reporting scrap. The GUI for this project gives the operator only relevant and critical information about their performance and the performance of their equipment leveraging high performance HMI techniques. With one terminal per machine placed immediately next to the line’s main control panel, the operator is given simple actions which are visible or invisible based on the current context. The management project acts as a desktop application for users to interact with the system when they are not operating equipment. It provides real time dashboards for individual process lines and groups of process lines, gives the user the ability to access reports with flexible time and datapoint selections, and provides intuitive GUI functionality for settings and configuration of the system.
The primary value-add of this system was moving to tracking and reporting OEE and downtime in real time. Previously, the facility was using a paper system with mechanical counters at the end of each line. A cycle counter would visit each machine every hour to gather 11” x 17” printed matrices recording downtime events and reset the mechanical counters. All of the data would then be aggregated by an analyst each day and spreadsheet-based reports were emailed out each morning. Moving to automated reporting of downtime events and machine-controlled counters significantly improved the accuracy of OEE metrics in addition to providing those metrics in real time for both management and the operators on the line.
Two Ignition projects were used to separate the ‘operator’ and ‘management’ functions of the application. The operator project includes features such as: starting and stopping production runs, setting downtime reason codes, and reporting scrap. The GUI for this project gives the operator only relevant and critical information about their performance and the performance of their equipment leveraging high performance HMI techniques. With one terminal per machine placed immediately next to the line’s main control panel, the operator is given simple actions which are visible or invisible based on the current context. The management project acts as a desktop application for users to interact with the system when they are not operating equipment. It provides real time dashboards for individual process lines and groups of process lines, gives the user the ability to access reports with flexible time and datapoint selections, and provides intuitive GUI functionality for settings and configuration of the system.
The primary value-add of this system was moving to tracking and reporting OEE and downtime in real time. Previously, the facility was using a paper system with mechanical counters at the end of each line. A cycle counter would visit each machine every hour to gather 11” x 17” printed matrices recording downtime events and reset the mechanical counters. All of the data would then be aggregated by an analyst each day and spreadsheet-based reports were emailed out each morning. Moving to automated reporting of downtime events and machine-controlled counters significantly improved the accuracy of OEE metrics in addition to providing those metrics in real time for both management and the operators on the line.
Track & Trace and OEE for 15 lines
South Carolina, US
The scope of this project was to provide error checking, production control, OEE, automated ERP
The scope of this project was to provide error checking, production control, OEE, automated ERP reporting, and material genealogy to a series of processes that produce high quality, high precision extruded cables. The final product included those features for 12 production lines and 3 rework lines within the facility, with the capability to add additional process and material types in the future. The ISA-95 production model includes over 400 objects with anywhere from 4 to 50 cells per line at varying levels of complexity of cell groups. The system design also significantly leverages supplemental equipment, work orders, and custom Process Segments and Operations Definitions.
Two Ignition projects were used to separate the ‘operator’ and ‘management’ functions of the application. The operator project includes features such as: starting and stopping production runs, scanning materials for lot number and quantity validation (via barcode scanning), in-process inspections, setting downtime reason codes, and reporting scrap. The GUI for this project gives the operator only relevant and critical information about their performance and the performance of their equipment leveraging high performance HMI techniques. With one terminal per machine placed immediately next to the line’s main control panel, the operator is given simple actions which are visible or invisible based on the current context. Additionally, the operator also has access to a mobile device which uses a mobile-optimized context-driven GUI to increase efficiency scanning/validating materials. The management project acts as a desktop application for users to interact with the system when they are not operating equipment. It provides real time dashboards for individual process lines and groups of process lines, gives the user the ability to access reports with flexible time and datapoint selections, and provides intuitive GUI functionality for settings and configuration of the system.
There were many value-adds as a result of this system’s implementation. Operators cannot start production with the incorrect or insufficient quantity of material; based on the characteristics of the process, this significantly reduces scrap and maximizes production floor efficiency. OEE is tracked automatically and instantly; this creates actionable data immediately so continuous improvement efforts are targeting the most significant problems. ERP reporting is done automatically; this reduces erroneous data sent to ERP by incorrect manual entry and saves operators (who were previously entering the data) time on the floor and reduces the number of systems the operator needs to be trained to use. Finally, the data and analysis tools (tracking how much material went where and when) gives support staff the data they need fast; because they have this data, they are able to drive changes all the way back to sales, purchasing, and production planning to reduce cost and waste throughout the facility.
Two Ignition projects were used to separate the ‘operator’ and ‘management’ functions of the application. The operator project includes features such as: starting and stopping production runs, scanning materials for lot number and quantity validation (via barcode scanning), in-process inspections, setting downtime reason codes, and reporting scrap. The GUI for this project gives the operator only relevant and critical information about their performance and the performance of their equipment leveraging high performance HMI techniques. With one terminal per machine placed immediately next to the line’s main control panel, the operator is given simple actions which are visible or invisible based on the current context. Additionally, the operator also has access to a mobile device which uses a mobile-optimized context-driven GUI to increase efficiency scanning/validating materials. The management project acts as a desktop application for users to interact with the system when they are not operating equipment. It provides real time dashboards for individual process lines and groups of process lines, gives the user the ability to access reports with flexible time and datapoint selections, and provides intuitive GUI functionality for settings and configuration of the system.
There were many value-adds as a result of this system’s implementation. Operators cannot start production with the incorrect or insufficient quantity of material; based on the characteristics of the process, this significantly reduces scrap and maximizes production floor efficiency. OEE is tracked automatically and instantly; this creates actionable data immediately so continuous improvement efforts are targeting the most significant problems. ERP reporting is done automatically; this reduces erroneous data sent to ERP by incorrect manual entry and saves operators (who were previously entering the data) time on the floor and reduces the number of systems the operator needs to be trained to use. Finally, the data and analysis tools (tracking how much material went where and when) gives support staff the data they need fast; because they have this data, they are able to drive changes all the way back to sales, purchasing, and production planning to reduce cost and waste throughout the facility.
OEE for Food Manufacturer: Site 1
Las Vegas, NV
9 Lines
110 Assets
ERP Connection for Materials, Rates, and Schedule
PLC Driven Downtime
Custom Metrics (OEE
9 Lines
110 Assets
ERP Connection for Materials, Rates, and Schedule
PLC Driven Downtime
Custom Metrics (OEE not being used)
2 Ignition Projects (Operator, Management)
Perspective Screens
The primary expectation of the customer was to have a supportable, unified, and consistent MES system between the sites. Having such a system drastically improves the ability to do cross-site analysis and share continuous improvement ideas developed from the data.
The customer had an existing home-grown intranet system where data had to be manually collected and was consistently wrong.
The automatic capture of data and having metrics easily available reduces the need for personnel to manually track equipment performance and downtime. This MES system was built to provide customer specific metrics but also maintain a standardization of the software and functionality between the sites. Operator buy-in was achieved by reducing the amount of paperwork and tasks that were required by the old methods.
Two Ignition projects were used to separate the ‘operator’ and ‘management’ functions of the application. The operator project includes features such as: automatic starting and stopping production runs and setting downtime reason codes. The GUI for this project gives the operator only relevant and critical information about their performance and the performance of their equipment leveraging high performance HMI techniques. With one terminal per machine placed immediately next to the line’s main control panel, the operator is given simple actions which are visible or invisible based on the current context. The management project acts as a desktop application for users to interact with the system when they are not operating equipment. It provides real time information for individual process lines and groups of process lines, gives the user the ability to access reports with flexible time and datapoint selections, and provides intuitive GUI functionality for settings and configuration of the system. The necessity of user interaction was kept to a minimum – lines automatically start and end runs, capture downtime, track line rates, and handle running changeovers.
The primary value-add of this system was reporting metrics and downtime in real time. Previously, the facilities were using multiple different methods to capture downtime and track production. Automatic reporting of downtime events and machine-controlled counters significantly improved the accuracy of their metrics in addition to providing those metrics in real time for both management and the operators on the line.
110 Assets
ERP Connection for Materials, Rates, and Schedule
PLC Driven Downtime
Custom Metrics (OEE not being used)
2 Ignition Projects (Operator, Management)
Perspective Screens
The primary expectation of the customer was to have a supportable, unified, and consistent MES system between the sites. Having such a system drastically improves the ability to do cross-site analysis and share continuous improvement ideas developed from the data.
The customer had an existing home-grown intranet system where data had to be manually collected and was consistently wrong.
The automatic capture of data and having metrics easily available reduces the need for personnel to manually track equipment performance and downtime. This MES system was built to provide customer specific metrics but also maintain a standardization of the software and functionality between the sites. Operator buy-in was achieved by reducing the amount of paperwork and tasks that were required by the old methods.
Two Ignition projects were used to separate the ‘operator’ and ‘management’ functions of the application. The operator project includes features such as: automatic starting and stopping production runs and setting downtime reason codes. The GUI for this project gives the operator only relevant and critical information about their performance and the performance of their equipment leveraging high performance HMI techniques. With one terminal per machine placed immediately next to the line’s main control panel, the operator is given simple actions which are visible or invisible based on the current context. The management project acts as a desktop application for users to interact with the system when they are not operating equipment. It provides real time information for individual process lines and groups of process lines, gives the user the ability to access reports with flexible time and datapoint selections, and provides intuitive GUI functionality for settings and configuration of the system. The necessity of user interaction was kept to a minimum – lines automatically start and end runs, capture downtime, track line rates, and handle running changeovers.
The primary value-add of this system was reporting metrics and downtime in real time. Previously, the facilities were using multiple different methods to capture downtime and track production. Automatic reporting of downtime events and machine-controlled counters significantly improved the accuracy of their metrics in addition to providing those metrics in real time for both management and the operators on the line.
OEE for Food Manufacturer: Site 2
Marlborough, MA
19 Lines
192 Assets
ERP Connection for Materials, Rates, and Schedule
PLC Driven Downtime
Custom Metrics (OEE not being
19 Lines
192 Assets
ERP Connection for Materials, Rates, and Schedule
PLC Driven Downtime
Custom Metrics (OEE not being used)
2 Ignition Projects (Operator, Management)
Perspective Screens
192 Assets
ERP Connection for Materials, Rates, and Schedule
PLC Driven Downtime
Custom Metrics (OEE not being used)
2 Ignition Projects (Operator, Management)
Perspective Screens
OEE for Food Manufacturer: Site 3
Lebanon, IN
8 Lines
91 Assets
ERP Connection for Materials, Rates, and Schedule
PLC Driven Downtime
Custom Metrics (OEE not
8 Lines
91 Assets
ERP Connection for Materials, Rates, and Schedule
PLC Driven Downtime
Custom Metrics (OEE not being used)
2 Ignition Projects (Operator, Management)
Perspective Screens
91 Assets
ERP Connection for Materials, Rates, and Schedule
PLC Driven Downtime
Custom Metrics (OEE not being used)
2 Ignition Projects (Operator, Management)
Perspective Screens
OEE for Plastics Manufacturer: Site 1
Nashville, TN
4 Months from Project Kick-Off to Go-Lives
6 Lines
179 Assets
ERP Connection for Materials, Rates, and Schedule
PLC
4 Months from Project Kick-Off to Go-Lives
6 Lines
179 Assets
ERP Connection for Materials, Rates, and Schedule
PLC Driven Downtime
Changeover Checklist
3 Ignition Projects (Operator, Management, Dashboard)
Proof-of-Concept Perspective Mobile Screens
The primary expectation of the customer was to have a supportable, unified, and consistent OEE system between the sites. Having such a system drastically improves the ability to do cross-site analysis and share continuous improvement ideas developed from the data.
The automatic capture of data and having metrics easily available reduces the need for personnel to manually track equipment performance and downtime.
Three Ignition projects were used to separate the ‘operator’, ‘management’ and ‘dashboard’ functions of the application. The operator project includes features such as: starting and stopping production runs, logging changeover checklists, and setting downtime reason codes. The GUI for this project gives the operator only relevant and critical information about their performance and the performance of their equipment leveraging high performance HMI techniques. With one terminal per machine placed immediately next to the line’s main control panel, the operator is given simple actions which are visible or invisible based on the current context. The management project acts as a desktop application for users to interact with the system when they are not operating equipment. It provides real time information for individual process lines and groups of process lines, gives the user the ability to access reports with flexible time and datapoint selections, and provides intuitive GUI functionality for settings and configuration of the system. The dashboard project is utilized on large TV’s throughout the facility. They show the production lines at-a-glance with the most important pieces of information.
The primary value-add of this system was moving to tracking and reporting OEE and downtime in real time. Previously, the facilities were using multiple different methods to capture downtime and track production. Automatic reporting of downtime events and machine-controlled counters significantly improved the accuracy of OEE metrics in addition to providing those metrics in real time for both management and the operators on the line.
6 Lines
179 Assets
ERP Connection for Materials, Rates, and Schedule
PLC Driven Downtime
Changeover Checklist
3 Ignition Projects (Operator, Management, Dashboard)
Proof-of-Concept Perspective Mobile Screens
The primary expectation of the customer was to have a supportable, unified, and consistent OEE system between the sites. Having such a system drastically improves the ability to do cross-site analysis and share continuous improvement ideas developed from the data.
The automatic capture of data and having metrics easily available reduces the need for personnel to manually track equipment performance and downtime.
Three Ignition projects were used to separate the ‘operator’, ‘management’ and ‘dashboard’ functions of the application. The operator project includes features such as: starting and stopping production runs, logging changeover checklists, and setting downtime reason codes. The GUI for this project gives the operator only relevant and critical information about their performance and the performance of their equipment leveraging high performance HMI techniques. With one terminal per machine placed immediately next to the line’s main control panel, the operator is given simple actions which are visible or invisible based on the current context. The management project acts as a desktop application for users to interact with the system when they are not operating equipment. It provides real time information for individual process lines and groups of process lines, gives the user the ability to access reports with flexible time and datapoint selections, and provides intuitive GUI functionality for settings and configuration of the system. The dashboard project is utilized on large TV’s throughout the facility. They show the production lines at-a-glance with the most important pieces of information.
The primary value-add of this system was moving to tracking and reporting OEE and downtime in real time. Previously, the facilities were using multiple different methods to capture downtime and track production. Automatic reporting of downtime events and machine-controlled counters significantly improved the accuracy of OEE metrics in addition to providing those metrics in real time for both management and the operators on the line.
OEE for Plastics Manufacturer: Site 2
Sidney, OH
4 Months from Project Kick-Off to Go-Lives
20 Lines
425 Assets
ERP Connection for Materials, Rates, and Schedule
PLC
4 Months from Project Kick-Off to Go-Lives
20 Lines
425 Assets
ERP Connection for Materials, Rates, and Schedule
PLC Driven Downtime
Changeover Checklist
3 Ignition Projects (Operator, Management, Dashboard)
Proof-of-Concept Perspective Mobile Screens
20 Lines
425 Assets
ERP Connection for Materials, Rates, and Schedule
PLC Driven Downtime
Changeover Checklist
3 Ignition Projects (Operator, Management, Dashboard)
Proof-of-Concept Perspective Mobile Screens
Multi-site OEE for Large Food Manufacturer
Project Description for 3 Sites With automatic batch-starting and SKU creation, the new system now reduces
Project Description for 3 Sites
With automatic batch-starting and SKU creation, the new system now reduces the time needed for configuration and maintenance. The customer can also create on-the-fly reports using the analysis selector tool. This tool helps users quickly identify issues with processes or equipment that need to be addressed for efficient production.
There are three major components to this project: operator screens, manager screens and dashboard view.
The operator screens let operators set up an automatic start time for batches. Because of this, operators then have time to work on startup tasks and manual stops (or manual starts if starting earlier than planned), change the scheduled rate according to the number of personnel on the line, and set downtime reason codes. Additionally, operators can control their assigned line and look at a read-only view of the entire site. This makes operators aware of any problems on related lines that may impact their own production.
The management screens give managers the ability to look at downtime history, production history and perform analyses. Managers also have access to a read-only version of the line as well as site overviews so they can see what is happening on the plant floor.
The dashboard view shows a simplified line status screen that is displayed on large monitors overhead. This view shows the production lines at a glance and highlights the most important pieces of information related to production.
The main benefit of this new system is in the capturing of run data. During a run, it is now easier than ever to see if a line is late to start or is running slowly and will not make its target. Managers and planners can also look at the data historically and plan accordingly by changing how batches are scheduled and executed to minimize unnecessary downtime.
Site 1 of 3
The customer’s primary expectation was to have their current high-cost OEE system replaced with a lower-cost solution that offered the same functionality as before along with the ability to add more features and MES modules.
The Sepasoft solution was rolled out to the first site in September 2019 and took two months from Project Kick-off to Go-Live. The next area was prepped for a future rollout at the same time.
With automatic batch-starting and SKU creation, the new system now reduces the time needed for configuration and maintenance. The customer can also create on-the-fly reports using the analysis selector tool. This tool helps users quickly identify issues with processes or equipment that need to be addressed for efficient production.
There are three major components to this project: operator screens, manager screens and dashboard view.
The operator screens let operators set up an automatic start time for batches. Because of this, operators then have time to work on startup tasks and manual stops (or manual starts if starting earlier than planned), change the scheduled rate according to the number of personnel on the line, and set downtime reason codes. Additionally, operators can control their assigned line and look at a read-only view of the entire site. This makes operators aware of any problems on related lines that may impact their own production.
The management screens give managers the ability to look at downtime history, production history and perform analyses. Managers also have access to a read-only version of the line as well as site overviews so they can see what is happening on the plant floor.
The dashboard view shows a simplified line status screen that is displayed on large monitors overhead. This view shows the production lines at a glance and highlights the most important pieces of information related to production.
The main benefit of this new system is in the capturing of run data. During a run, it is now easier than ever to see if a line is late to start or is running slowly and will not make its target. Managers and planners can also look at the data historically and plan accordingly by changing how batches are scheduled and executed to minimize unnecessary downtime.
Site 1 of 3
The customer’s primary expectation was to have their current high-cost OEE system replaced with a lower-cost solution that offered the same functionality as before along with the ability to add more features and MES modules.
The Sepasoft solution was rolled out to the first site in September 2019 and took two months from Project Kick-off to Go-Live. The next area was prepped for a future rollout at the same time.
2019-09-01 - 2019-10-31
Multi-site OEE for Large Food Manufacturer
Site 2 of 3 The customer’s primary expectation was to have their current high-cost OEE system
Site 2 of 3
The customer’s primary expectation was to have their current high-cost OEE system replaced with a lower-cost solution that offered the same functionality as before along with the ability to add more features and MES modules.
The second site switched over to the Sepasoft solution in October 2019, which took two months from Project Kick-off to Go-Live. This site includes very automated canning lines as well as the more manually-involved pizza and entrée lines.
The customer’s primary expectation was to have their current high-cost OEE system replaced with a lower-cost solution that offered the same functionality as before along with the ability to add more features and MES modules.
The second site switched over to the Sepasoft solution in October 2019, which took two months from Project Kick-off to Go-Live. This site includes very automated canning lines as well as the more manually-involved pizza and entrée lines.
2019-10-15 - 2019-12-16
Multi-site OEE for Large Food Manufacturer
The customer’s primary expectation was to expand their replacement MES system, which we previously installed
The customer’s primary expectation was to expand their replacement MES system, which we previously installed on two other sites, to a third site. This was their first system on site for OEE and downtime tracking.
This site underwent startup in November 2019 and was the final of the three sites. It took two weeks from Project Kick-off to Go-Live. The plant is the smallest of the sites and includes canning and frozen entrée assembly and packaging. It was the first site to include large dashboard monitors above the lines so anyone on the plant floor could see very quickly how the batch was progressing. These were later deployed to the other sites.
This site underwent startup in November 2019 and was the final of the three sites. It took two weeks from Project Kick-off to Go-Live. The plant is the smallest of the sites and includes canning and frozen entrée assembly and packaging. It was the first site to include large dashboard monitors above the lines so anyone on the plant floor could see very quickly how the batch was progressing. These were later deployed to the other sites.
2019-11-30 - 2019-12-13
OEE for Pharma
Swiftwater, Pennsylvania
Sanofi's OEE system serves as a solution for optimizing the filling process for immunizations production
Sanofi's OEE system serves as a solution for optimizing the filling process for immunizations production at their Swiftwater, Pennsylvania facility which specializes in Flu and Covid immunization manufacture. It makes use of data collected from OSI PI and extensive perspective based dashboards detailing production and changeover performance for pharmaceutical processes.
Locations
Irvine, CA
US
PHOENIX, AZ
US
Austin, TX
US
Nashville, TN
US
Contact
David Folkner

OEE Gold Certified
5 Engineers

OEE Certified
7 Engineers

OEE Credentialed
6 Engineers

SPC Gold Certified
1 Engineer

SPC Certified
2 Engineers

SPC Credentialed
6 Engineers

Settings & Changeover Certified
3 Engineers

Settings & Changeover Credentialed
6 Engineers

Track & Trace Gold Certified
3 Engineers

Track & Trace Certified
3 Engineers

Track & Trace Credentialed
3 Engineers

Business Connector Gold Certified
1 Engineer

Business Connector Credentialed
5 Engineers

Interface for SAP ERP Gold Certified
1 Engineer