Brock Solutions Inc
Sepasoft MES Gold Integrator
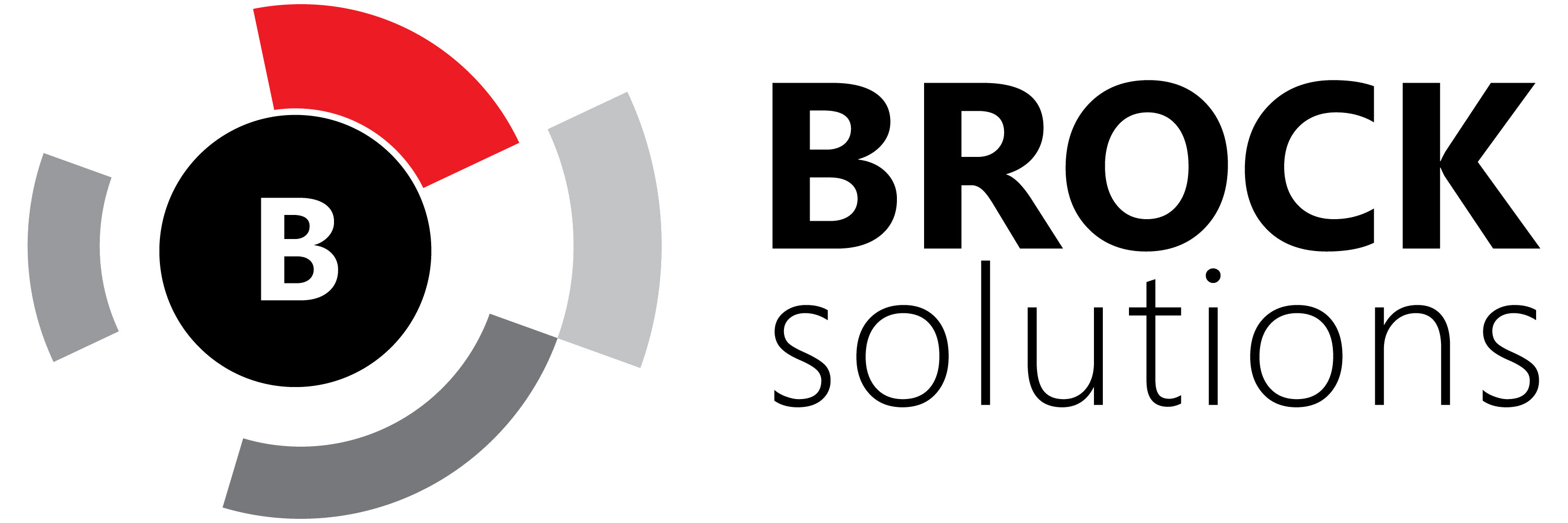
Brock Solutions is an engineering and professional services company focused on improving the operations of Manufacturing, Transportation, and Logistics organizations by taking a holistic approach to the implementation of innovative technology solutions. Since its inception in 1985, Brock has grown to become the largest independent real-time systems integrator in North America with 10,000+ projects completed worldwide, a team of 600 connected professionals, and multiple office locations throughout the US and Canada.
MES Certifications
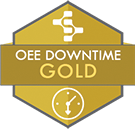
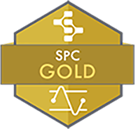
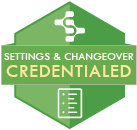
3 Gold AND 2 Credentialed MES ENGINEERS
1 LOCATIONS
Projects
Modernization and Realiability with SPC
USA
The project was to develop a solution using Ignition which would connect to existing sampling
The project was to develop a solution using Ignition which would connect to existing sampling hardware and provide SPC trend to the users in real time. The existing system was a legacy implementation running on outdated hardware and excel macros. Modernization was a driving factor as well as reliability and extending the available features of the system.
The Sepasoft SPC module was leveraged for its ability to configure and collect samples and displaying SPC visualizations of those records in real time. This project required integration for the physical sampling machines to extract the sample records and save them into the module without manual interaction. The application was connected to devices to record two unique sample types each with several parameters.
Further integration was performed to handle the limits for the SPC trends. Sample limited were pulled from the customers production definition system and pushed out to the configured devices. This change to the process removed the manual steps previously required to enter the spec limits of an active run.
Benefits from the deployment have been overall system stability, improved historical data, removal of manual limit entry, and modernization of the supporting infrastructure.
The Sepasoft SPC module was leveraged for its ability to configure and collect samples and displaying SPC visualizations of those records in real time. This project required integration for the physical sampling machines to extract the sample records and save them into the module without manual interaction. The application was connected to devices to record two unique sample types each with several parameters.
Further integration was performed to handle the limits for the SPC trends. Sample limited were pulled from the customers production definition system and pushed out to the configured devices. This change to the process removed the manual steps previously required to enter the spec limits of an active run.
Benefits from the deployment have been overall system stability, improved historical data, removal of manual limit entry, and modernization of the supporting infrastructure.
Real-Time Production Data with OEE
USA
The project has developed into a continuous program through the partnership between Brock Solutions and
The project has developed into a continuous program through the partnership between Brock Solutions and our customer. The initial use case was to augment their existing MES platform to enhance the availability of production information to drive business decisions.
The core objective was to improve the access to reliable data from the plant floor and create a system which would deliver this information to the manufacturing operations team in real time. This system needed to provide production information along with downtime and stop reasons to help the engineering group address equipment issues.
Leveraging the Sepasoft OEE_Downtime_V2 module the plant was modeled to collect this detailed information from all 72 of the production complexes, each with several production cells. Having this information available within Ignition allowed further extensions of the application to support a new continuous improvement program, maintenance scheduling and reporting of plant wide KPI metrics.
The application now supports around 100 concurrent clients on average. The application has been widely adopted as an extension of their manufacturing systems, integrating into the daily activities of many roles across the production facility, including operators, area supervisors, maintenance and CI teams.
Benefits from the deployment have been reductions in labor hours for data collection and manipulation, and digitizing paperwork for scheduling and reporting. It has also provided consistency between areas and shifts by consolidating all actions through a single application instead of SharePoint documents.
The core objective was to improve the access to reliable data from the plant floor and create a system which would deliver this information to the manufacturing operations team in real time. This system needed to provide production information along with downtime and stop reasons to help the engineering group address equipment issues.
Leveraging the Sepasoft OEE_Downtime_V2 module the plant was modeled to collect this detailed information from all 72 of the production complexes, each with several production cells. Having this information available within Ignition allowed further extensions of the application to support a new continuous improvement program, maintenance scheduling and reporting of plant wide KPI metrics.
The application now supports around 100 concurrent clients on average. The application has been widely adopted as an extension of their manufacturing systems, integrating into the daily activities of many roles across the production facility, including operators, area supervisors, maintenance and CI teams.
Benefits from the deployment have been reductions in labor hours for data collection and manipulation, and digitizing paperwork for scheduling and reporting. It has also provided consistency between areas and shifts by consolidating all actions through a single application instead of SharePoint documents.
Locations
Kitchener, Ontario
CA
Contact
Ryan Dyni

OEE Gold Certified
3 Engineers

OEE Credentialed
1 Engineer

SPC Gold Certified
2 Engineers

Settings & Changeover Credentialed
1 Engineer